Final Drive for Excavators: A Comprehensive Guide to Understanding and Maintenance
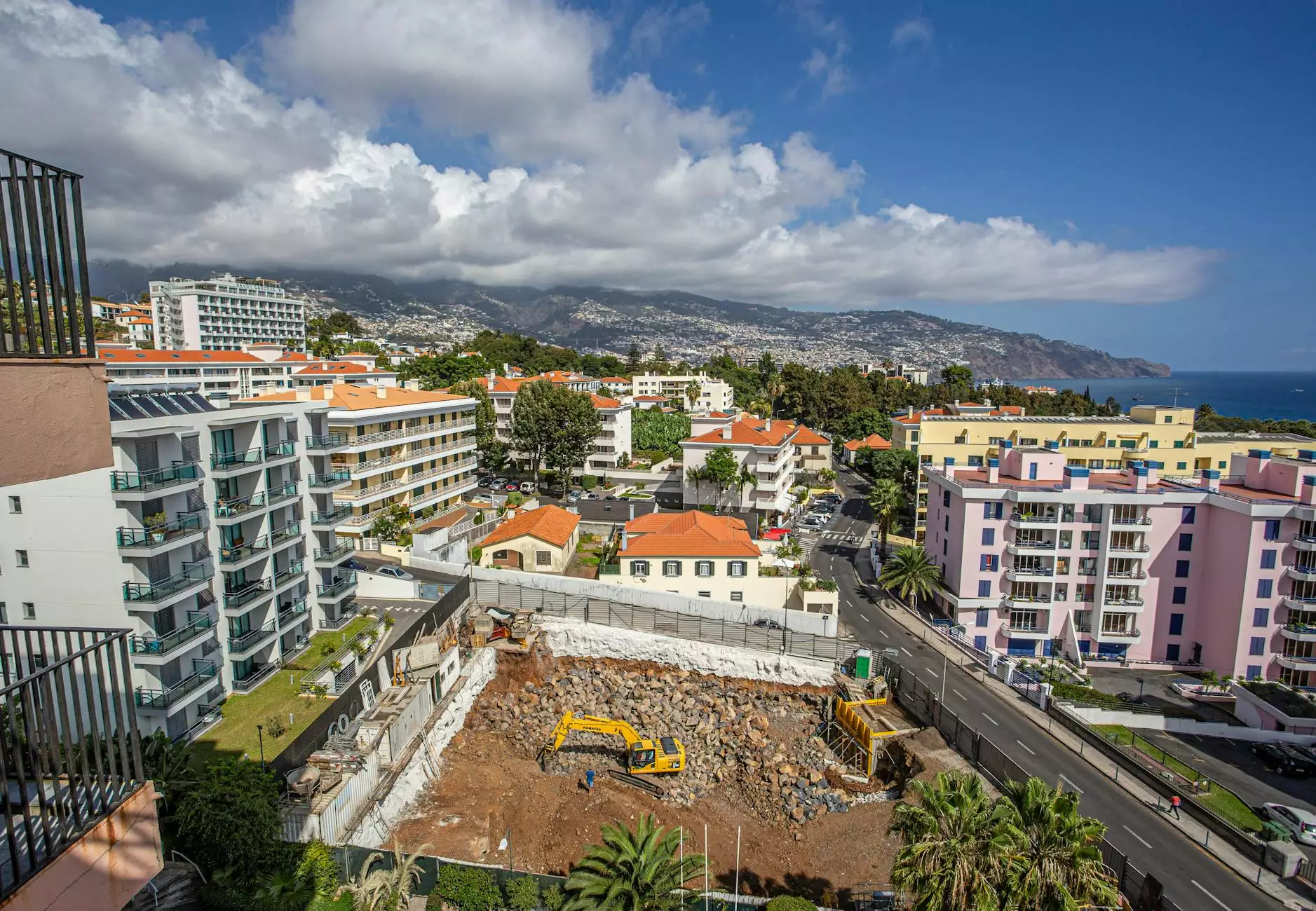
The final drive for excavators is a critical component that plays a significant role in the overall performance and efficiency of excavators. Its main function is to transfer power from the machine’s engine to the track drive system, allowing for the smooth operation of various excavation tasks. In this extensive guide, we will explore everything related to final drives, helping you understand their importance, how they function, and how to maintain them for optimal performance.
What is a Final Drive?
The final drive is essentially a gearbox located on each track side of an excavator. It converts the high-speed, low-torque rotation from the engine into the low-speed, high-torque rotation needed to drive the tracks effectively. The design of a final drive is meant to optimize power delivery while also providing sufficient speed and maneuverability for the machine.
Key Components of a Final Drive
Understanding the individual parts of a final drive for excavators can help operators and technicians troubleshoot problems and perform maintenance accurately. The main components typically include:
- Gearbox: Transforms engine speed and torque.
- Hydraulic Motor: Drives the gearbox and provides the necessary force.
- Sprocket: Connects the final drive to the tracks.
- Seals: Prevent contamination and fluid leaks.
- Bearings: Support the internal components allowing for smooth operation.
Types of Final Drives for Excavators
There are primarily two types of final drives used in excavators:
- Planetary Gear Final Drive: This type is known for its compact design and is prevalent in mini-excavators. It uses planetary gears to distribute load and offers high durability.
- Spur Gear Final Drive: Typically found in larger machines, the spur drive has a more straightforward design and can handle higher torque levels, making it suitable for heavy-duty applications.
How Does a Final Drive Work?
The operation of a final drive can be broken down into a few simple steps:
- The engine generates power and sends it to the hydraulic system.
- The hydraulic motor receives this power and converts it into mechanical energy.
- This energy is transmitted to the gearbox, which alters the speed and torque.
- The output of the gearbox is connected to the tracks via the sprocket, causing the tracks to move.
Importance of Maintaining Your Final Drive
Proper maintenance of the final drive is crucial for ensuring the longevity and efficiency of your excavator. Here are some reasons why regular upkeep is important:
- Prevention of Major Failures: Regular checks help identify wear and tear before it leads to costly repairs.
- Enhanced Performance: A well-maintained final drive ensures that the excavator operates at optimal efficiency.
- Lower Operational Costs: Preventive maintenance can significantly reduce downtime and repair costs.
Signs of a Failing Final Drive
Even with proper maintenance, final drives can experience issues. Here are some warning signs that may indicate a problem:
- Unusual Noises: Grinding or whining sounds while operating can point to internal failures.
- Loss of Power: A noticeable decrease in power to the tracks may indicate failing hydraulic components.
- Fluid Leaks: Signs of hydraulic fluid leaks around the seals can lead to continued fluid loss and eventual failure.
- Vibration: Excessive vibration during operations can indicate worn bearings or misalignment in the gearbox.
How to Maintain Your Final Drive
Regular maintenance of the final drive includes several key practices:
1. Regular Inspections
Schedule routine inspections to check for signs of wear, leaks, and other damage. This proactive approach can prevent breakdowns.
2. Fluid Changes
Replacing the hydraulic fluid at recommended intervals is essential for keeping the hydraulic motor and gearbox functioning correctly. Contaminated fluid can cause serious damage to internal components.
3. Monitor Operating Conditions
Keep an eye on the operating environment. Heavy dust or mud can lead to premature wear. Use appropriate filters and regularly replace them to ensure clean fluid flow.
4. Lubrication
Ensure that all moving parts are well-lubricated. Proper lubrication extends the life of bearings and gears, reducing friction and wear.
Choosing the Right Final Drive for Your Excavator
When it comes to selecting a final drive for your excavator, it’s crucial to consider several factors:
- Compatibility: Ensure the final drive is compatible with your specific excavator model.
- Quality: Opt for high-quality parts from reputable manufacturers to ensure reliability and durability.
- Torque Requirements: Match the final drive specifications with the torque requirements of your excavator.
- Warranty and Support: Consider products that come with good warranty coverage and customer support.
Final Thoughts: The Essential Role of Final Drives in Excavators
In conclusion, the final drive for excavators is not just a component; it's the backbone of the machine's mobility and efficiency. Understanding its function, recognizing the signs of wear, and performing regular maintenance can dramatically affect your excavator's performance and longevity. Make informed decisions while selecting replacement parts and always prioritize quality and compatibility. By doing so, you can enhance your excavation operations and ensure that your machinery stands the test of time.
Shop Quality Final Drives at Shop Hydraulic America
If you are in the market for a reliable final drive for your excavator, consider visiting Shop Hydraulic America. They offer an extensive range of auto parts and supplies, including high-quality motorcycle parts, ensuring you find exactly what you need for your machinery. Their commitment to customer satisfaction and quality products makes them a trusted choice for many operators.
© 2023 Shop Hydraulic America. All rights reserved.