Accelerating Innovation: The Impact of Rapid Prototype in Metal Fabrication
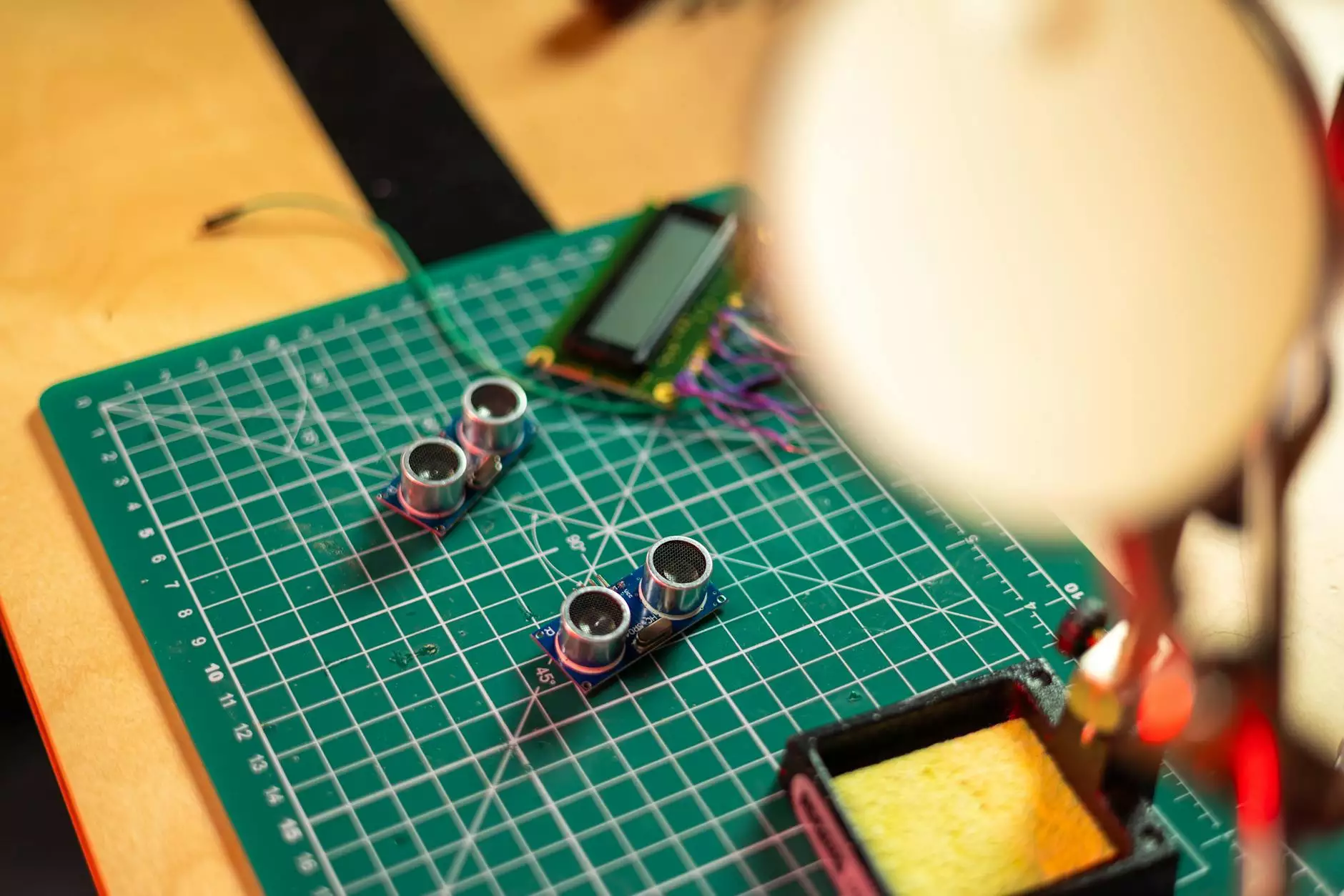
In the highly competitive world of metal fabrication, businesses are constantly searching for ways to enhance their processes, reduce costs, and accelerate time-to-market. One transformative approach that has emerged in recent years is rapid prototyping. This article will delve deep into how rapid prototype technologies are reshaping the landscape of metal fabrication, bringing forth unparalleled efficiencies and innovations.
What is Rapid Prototyping?
At its core, rapid prototyping refers to a group of techniques used to quickly create a physical model or prototype of a product using computer-aided design (CAD) data. The primary goal is to reduce the time it takes to turn an idea into a tangible product. In metal fabrication, this can involve various processes such as:
- 3D Printing: Utilizing additive manufacturing to create intricate designs layer by layer.
- CNC Machining: Employing computer numerical control to achieve precision in cutting and shaping metal.
- Sheet Metal Fabrication: Forming metal sheets into desired shapes quickly and accurately.
- Die Casting and Injection Molding: Producing parts at scale while maintaining high quality.
The Benefits of Rapid Prototyping in Metal Fabrication
The integration of rapid prototype techniques into metal fabrication processes offers numerous benefits that can significantly enhance business operations:
1. Reduced Time-to-Market
One of the most significant advantages of rapid prototyping is the dramatic reduction in time to produce new products. Instead of traditional prototyping methods that can take weeks or even months, rapid prototyping can often produce a functional prototype in a matter of days. This accelerated development cycle allows companies to:
- Quickly test ideas and gather feedback.
- Make informed decisions based on real-world product performance.
- Stay ahead of competitors by launching products faster.
2. Cost Efficiency
Implementing rapid prototype techniques can lead to significant cost savings. The traditional process of creating prototypes can be resource-intensive, often requiring expensive materials and extensive labor. In contrast, rapid prototyping allows companies to:
- Minimize waste by using only the necessary materials.
- Reduce labor costs through automated processes.
- Avoid costly mistakes by allowing for iterative testing.
3. Enhanced Design Flexibility
Another remarkable advantage of rapid prototyping is the flexibility it offers in design modifications. In the past, altering a design after the prototype stage could be a lengthy and costly task. However, with rapid prototyping, modifications can be made swiftly, enabling designers to:
- Experiment with various designs and materials.
- Respond to client feedback quickly.
- Optimize the final product for performance and aesthetics.
4. Improved Communication and Collaboration
Prototyping acts as a visual aid that bridges the gap between designers, engineers, and stakeholders. With a tangible model made through rapid prototype methods, communication improves significantly. Teams can:
- Visualize ideas more effectively.
- Identify potential issues early in the development process.
- Align on goals and expectations with greater clarity.
Emerging Technologies in Rapid Prototyping
The field of rapid prototyping is continuously evolving, with new technologies emerging that expand its capabilities. Some of the most exciting advancements include:
1. Advanced Materials
New material developments are paving the way for stronger, lighter, and more cost-effective prototypes. Innovations in metal alloys, plastics, and composites are allowing fabrication companies to harness properties that were previously unattainable.
2. Hybrid Manufacturing
Hybrid manufacturing combines traditional techniques with rapid prototyping capabilities. This approach allows manufacturers to utilize the strengths of both methods, achieving intricate designs with enhanced strength and durability.
3. Artificial Intelligence (AI)
The integration of AI into rapid prototyping processes can facilitate smarter design iterations and optimizations. AI algorithms can analyze prototypes for weaknesses and propose improvements, further reducing development time and costs.
Case Studies: Success Stories in Rapid Prototyping
To understand the practical application of rapid prototype techniques in metal fabrication, let’s explore a couple of success stories:
Case Study 1: Automotive Industry
A leading automotive manufacturer implemented rapid prototyping to streamline their development of components. By using 3D printing technology, they were able to produce functional prototypes in just a week, allowing for quicker testing and validation of new designs. This process led to:
- A 30% reduction in development time.
- A significant decrease in prototype costs.
- Enhanced collaboration between design and engineering teams.
Case Study 2: Aerospace Sector
An aerospace company adopted rapid prototyping for producing parts for aircraft. Utilizing CNC machining alongside 3D printing, they could fabricate complex geometries that were previously impossible with traditional methods. The results included:
- Increased performance due to optimized weight reductions.
- Faster compliance with regulatory standards through iterative testing.
- Higher customer satisfaction owing to improved product quality.
Challenges in Adopting Rapid Prototyping
While the benefits of rapid prototype techniques are compelling, there are challenges associated with their adoption that businesses must navigate, including:
1. Initial Investment Costs
Implementing rapid prototyping technologies often requires a significant upfront investment in equipment and training. Companies must evaluate the long-term benefits against these initial costs.
2. Skill Gaps
With rapid advancements in technology, existing workforce skills may not always align with new requirements. Companies might need to invest in continuous training and hiring to keep pace.
3. Quality Control
Ensuring consistent quality in prototypes produced via rapid prototyping methods can be challenging, especially when using new materials or processes. Rigorous testing and quality control measures must be implemented to mitigate risks.
The Future of Rapid Prototyping in Metal Fabrication
The future of rapid prototyping in metal fabrication looks exceptionally promising. As technology continues to advance, we can anticipate:
1. Greater Automation
Automation technologies will enhance rapid prototyping processes, enabling manufacturers to achieve higher output rates while maintaining quality.
2. Sustainable Practices
With the growing emphasis on sustainability, we can expect rapid prototyping practices to evolve towards more eco-friendly materials and processes, reducing waste and energy consumption.
3. Widespread Adoption
As the benefits of rapid prototyping become more evident, its adoption across various industries will likely increase. This adoption will facilitate innovation and provide businesses with the tools necessary to thrive in an increasingly competitive landscape.
Conclusion
To succeed in today’s fast-paced industrial environment, leveraging rapid prototype technologies is not just an option; it's essential. With the potential to reduce time, cut costs, enhance design flexibility, and improve collaboration, rapid prototyping is revolutionizing the metal fabrication industry. Businesses that embrace this innovative approach position themselves for success, driving forward with efficiency, creativity, and a competitive edge.
As we look ahead, the possibilities for rapid prototyping are limitless. Companies like Deep Mould are at the forefront of this transformation, demonstrating how innovation can lead to unprecedented growth and success in metal fabrication.