The Vital Role of Automotive Injection Molding Companies in Today's Automotive Industry
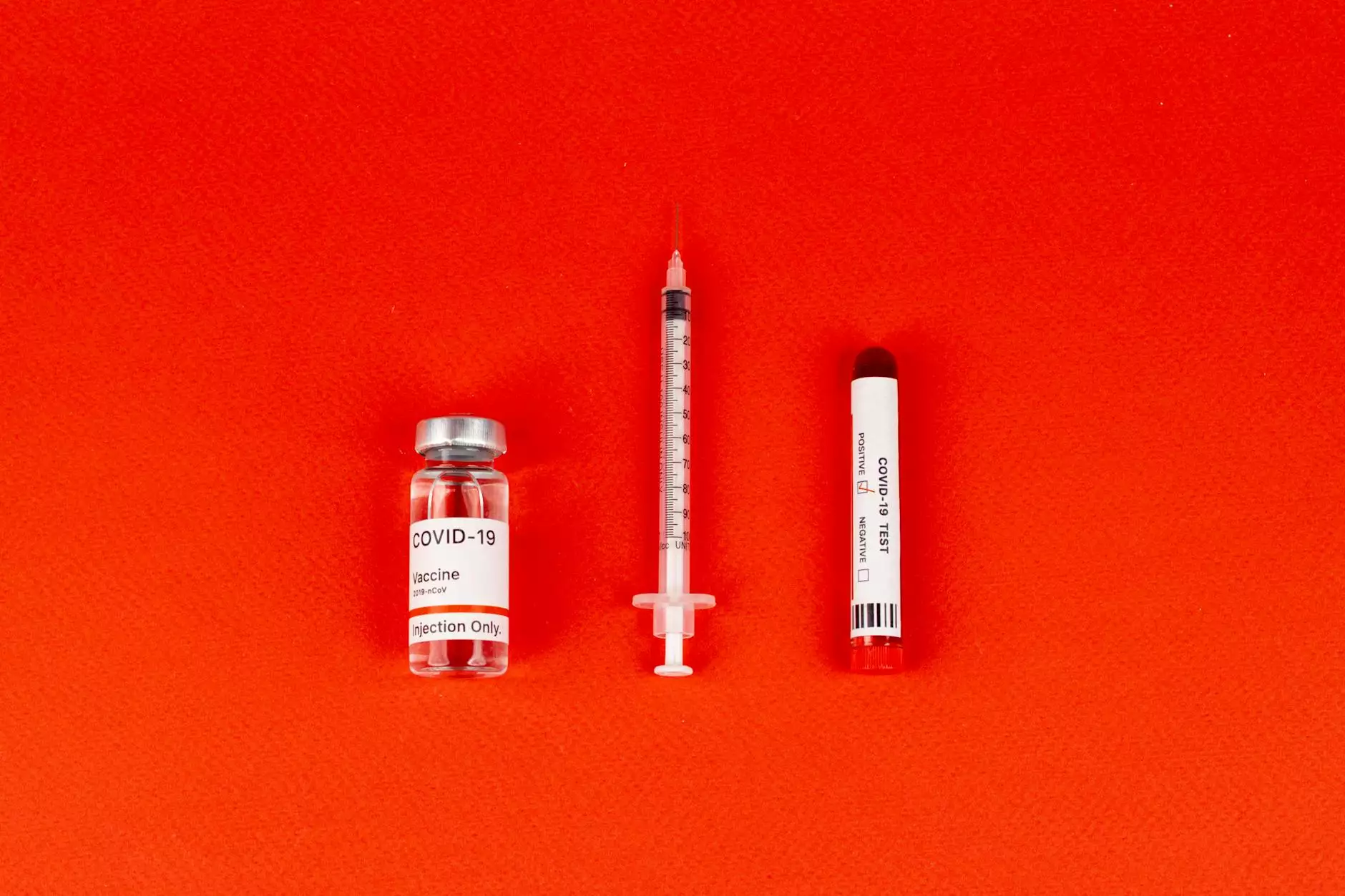
Automotive injection molding companies are at the forefront of innovation in the automotive industry. As vehicles become more complex and demanding in terms of design and functionality, these companies emerge as essential players supporting advancements through their expertise in plastic tooling and molding processes. This article explores the intricacies of these companies, their processes, and their impact on the automotive sector.
What is Automotive Injection Molding?
Injection molding is a manufacturing process used to produce parts by injecting molten material into a mold. This technique is especially popular in the automotive sector due to its ability to create intricate and precise components efficiently. The materials commonly used for injection molding include various types of plastics, which provide essential properties such as durability, lightweight, and resilience to heat and chemicals.
Why Choose Automotive Injection Molding?
There are several reasons why automotive manufacturers rely heavily on injection molding processes:
- Cost-Effectiveness: Once the molds are created, the cost of production per unit decreases significantly, making it a favorable option for mass production.
- Precision and Accuracy: Injection molding allows for tight tolerances and consistency across produced parts, which is critical in automotive applications.
- Complex Geometries: This process is capable of creating complex shapes that are often required in modern automobile designs.
- Material Versatility: A variety of materials can be utilized, including thermoplastics, thermosets, and composite materials, allowing for different properties and cost considerations.
Key Processes Involved in Automotive Injection Molding
The operation of a typical automotive injection molding company encompasses several critical stages:
1. Design and Prototype Development
The initial phase involves designing the component using CAD (Computer-Aided Design) software. Prototypes are created to evaluate the design's functional and aesthetic qualities.
2. Mold Creation
Once the design is approved, mold making begins. Custom molds are crafted from metals such as steel or aluminum, which can withstand the high pressures and temperatures experienced during the injection molding process.
3. Material Selection
The right material is crucial—companies select from various thermoplastics to thermoforming polymers, depending on the part's intended use, durability, and environmental exposure.
4. Injection Molding Process
The selected material is heated until it becomes molten and is then injected into the mold. Once cooled, the mold is removed, and the finished part is ejected.
Applications of Automotive Injection Molding
Automotive injection molding companies supply a vast range of components for vehicles, including:
- Interior Components: Dashboard panels, door handles, and seat components.
- Exterior Parts: Bumpers, fenders, and trim pieces.
- Functional Parts: Clips, brackets, and connectors that enhance the mechanical functioning of various systems.
The Future of Automotive Injection Molding
As the automotive industry transitions towards electric vehicles and sustainable practices, the role of automotive injection molding companies will evolve. Innovations in materials and technology are likely to emerge, including:
- Biodegradable Materials: To meet environmental standards and consumer demand for sustainability, companies are investigating bio-based plastics that reduce environmental impact.
- Lightweight Materials: With the push for energy efficiency, there is a growing emphasis on lighter materials that can reduce the overall weight of the vehicle.
- Advanced Manufacturing Technologies: Implementing automation and AI in the injection molding process will lead to increased efficiency and quality control.
Challenges Faced by Automotive Injection Molding Companies
While the advantages are plentiful, there are also significant challenges that these companies must navigate:
- High Initial Costs: The development of molds and setup for production can require substantial investment.
- Market Volatility: Fluctuations in automotive demand and material prices can challenge companies to remain profitable.
- Environmental Regulations: Stricter regulations on waste and emissions require ongoing compliance efforts and innovative solutions.
Conclusion
In conclusion, automotive injection molding companies play a crucial role in shaping the future of the automotive industry. Their ability to produce high-quality, complex parts at scale allows manufacturers to innovate continuously while adhering to safety and environmental standards. As technology advances and the industry shifts towards sustainability, these companies are poised to lead the way in creating a modern, efficient, and environmentally conscious automotive landscape.
About DeepMould.net
DeepMould is a leading name among automotive injection molding companies, specializing in providing precision-engineered components that meet the highest industry standards. With a commitment to innovation, quality, and customer satisfaction, DeepMould is proud to be at the heart of automotive manufacturing, paving the way for future advancements.
© 2023 DeepMould.net. All rights reserved.